Partner in Pet Food
Przykład udanej cyfryzacji Partner in Pet Food dzięki MES SoftLI
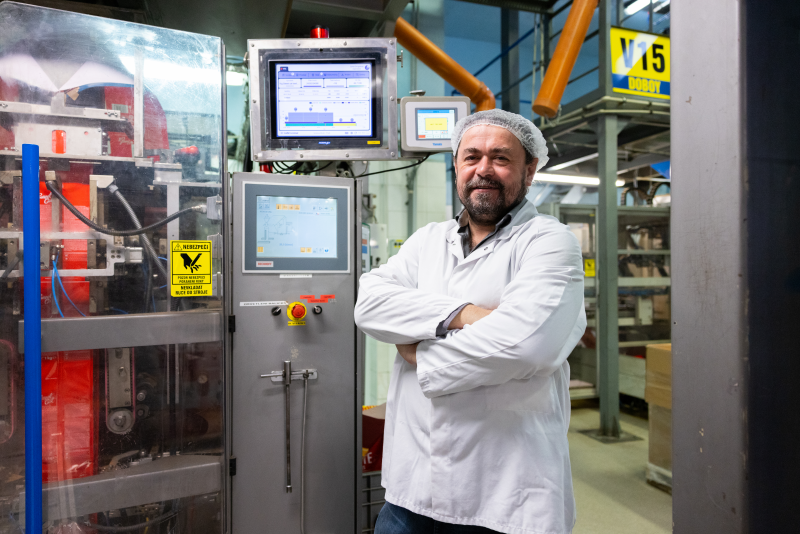
MES SoftLi jest już z sukcesem wykorzystywany przez wiele liczących się firm z różnych branż w celu usprawnienia produkcji. Jednym z nich jest Partner in Pet Food – wiodący producent karmy dla zwierząt domowych, działający w 10 krajach Europy. Naczelną wartością firmy jest kultura korporacyjna oparta na efektywności i umiejętności znajdowania rozwiązań w każdej sytuacji. Jest to spójne z działaniem MES SoftLI. Nic więc dziwnego, że współpraca układa się świetnie. O szczegóły zapytaliśmy kierownika produkcji PPF, Zdenka Zahejskiego.
Kiedy zacząłeś myśleć o cyfryzacji produkcji?
Prawdopodobnie zaraz po tym, jak dołączyłem do PPF 6 lat temu, kiedy cała dokumentacja produkcyjna prowadzona była jeszcze w formie papierowej. A w niektórych obszarach w ogóle jej nie było. To była duża różnica w porównaniu do mojego poprzedniego miejsca pracy, gdzie korzystaliśmy z systemów monitorowania produkcji na wtryskarkach.
Czy możesz porównać ówczesną sytuację z dzisiejszą?
Myślę, że dzięki temu, co tutaj wdrożyliśmy, jesteśmy znacznie dalej niż zdecydowana większość dzisiejszych firm.
Jak przebiegała cyfryzacja produkcji?
Najpierw wdrożyliśmy MES SoftLi. Jest to system gromadzenia danych, na podstawie którego możemy oceniać dane i sporządzać analizy lub raporty, zarówno dla nas, jak i dla zarządu i właścicieli firmy.
Wkrótce po wypróbowaniu MES stwierdziliśmy, że jest on dla nas przydatny, wygodny i zadowolony z zarządzania. Dlatego postanowiliśmy go dalej rozwijać i sukcesywnie wdrażaliśmy coraz więcej modułów, aż udało nam się zbudować stosunkowo solidny system, który dziś nie ma analogii w grupie PPF. Często po inspirację przychodzą do nas koledzy z innych fabryk – i opowiadam im, jak dzięki temu MES-owi znacznie usprawniliśmy produkcję.
Co najbardziej interesuje kolegów z zagranicy?
Zwykle zależy to od zawodu, ponieważ kierownika produkcji interesują inne moduły niż inżyniera jakości. Wszyscy, łącznie z wyższą kadrą kierowniczą, są pod ogromnym wrażeniem, gdy pokazuję im, że zawsze jestem online, że przez cały czas widzę ekran operatora w czasie rzeczywistym i że w każdej chwili mogę pokazać im aktualne raporty.
Twoja firma stawia na maksymalną elastyczność w każdym obszarze, aby była jak najbardziej efektywna. Czy dostosowałeś także MES?
Tak, we współpracy z SoftLi zmodyfikowaliśmy pewne rzeczy w systemie tak, aby MES w pełni odpowiadał naszym, bardzo specyficznym potrzebom. W pełni zintegrowaliśmy i połączyliśmy go z naszym systemem ERP. Dziś oba systemy działają w pełnej symbiozie i automatycznie wymieniają między sobą niezbędne dane.
Czy możesz podać przykład takiej komunikacji pomiędzy systemami?
Z MES np. zapisujemy dane bezpośrednio do ERP, natomiast z ERP pobieramy dane z zestawień materiałowych. Jest tego naprawdę dużo, bo jak już mówiłem – dzisiejszy system jest naprawdę solidny i dopracowany w najdrobniejszych szczegółach. I to właśnie daje nam znaczącą przewagę nad konkurencją.
Masz również wdrożony system planowania, prawda?
Tak. Wstrzymaliśmy go do samego końca. Z perspektywy czasu pewnie mogę to przyznać, ale bardzo się bałam, że to nie wyjdzie.
Dlaczego?
Podobnie było w moim poprzednim miejscu pracy. Próbowaliśmy tego dwa razy - i dwa razy zrezygnowaliśmy, ponieważ było to zbyt skomplikowane zarówno dla planistów, jak i producentów. Było to dla nich bardzo zagmatwane i mimo to woleli pracować w Excelu. Zawsze wracaliśmy do Excela, bo tak było łatwiej.
Co wyróżniało PPF?
System produkcji był podobny. Zaplanowano to także w ERP połączonym z Excelem i nie było wykresu Gantta ani wizualizacji. Jednak zasadnicza różnica dotyczyła dostawcy MES i jego wdrożenia.
Z SoftLi od samego początku wyjaśniliśmy sobie nawzajem możliwości i oczekiwania. Określiliśmy, czego oczekujemy od systemu, a następnie dostosowaliśmy to do naszych potrzeb. Oczywiście proces ten podlega pewnemu rozwojowi i dopracowanie go w 100% zajęło trochę czasu, ale dziś jest już na dobrej drodze. Bardzo mnie to cieszy, bo dla mnie to pierwsza instalacja planera, który naprawdę sprawdza się w praktyce i z którego chętnie korzystają wszyscy pracownicy.
Jako menadżer zawsze chcę zapobiegać sytuacjom, w których przełożony coś narzuca, a podwładni z tego nie korzystają, bo zamiast ułatwiać pracę, traktują to jako ciężar i próbują znaleźć jakieś wyjście, ale codziennie widzę ludzi pracujących z MES SoftLi. Na porannym spotkaniu pokazywane są dane z poprzedniego dnia, które od razu analizujemy. Planiści natomiast lubią korzystać z planera, który ułatwia im życie. Ta pozytywna zmiana znajduje odzwierciedlenie także w innych działach, gdzie np. po prostu monitorują, kiedy każde zamówienie zostanie wysłane.
Jako menadżer cieszę się, że MES u nas „żyje” i że pracownicy przyjęli go jak swój. Dostrzegają, że jest im to potrzebne do pracy i że dziś jest to w zasadzie konieczność.
Więc w ogóle nie używasz już Excela?
Używamy już Excela tylko do niektórych wyników. Ale to dlatego, że operatorzy na produkcji od wielu lat są przyzwyczajeni do Excelowego systemu przekazywania planu produkcji i dlatego jeszcze tego nie ruszałem. Postanowiłem wdrożyć to w łagodniejszy sposób. Idę krok po kroku i stopniowo przekonuję ludzi do konieczności zmiany.
Każde kolejne wdrożenie jest coraz łatwiejsze, bo pracownicy rozumieją, po co to robimy, i że zmiana ułatwi im pracę. Musi to po prostu naturalnie przeniknąć do poziomu ostatniego operatora, zanim przejdziemy do całkowitej cyfryzacji.
Czy współpracujecie z SoftLi również na tym etapie pośrednim?
Tak, opracowaliśmy taki etap pośredni, podczas którego ten doświadczony arkusz Excel jest generowany bezpośrednio z planisty. Dzięki temu planista nie musi wpisywać go ręcznie. Następnym etapem będzie całkowite usunięcie Excela z naszego przepływu pracy. Operatorzy mający dostęp do klientów internetowych będą mieli wgląd bezpośrednio do planisty i będą mogli bezpośrednio zobaczyć, co się dzieje.
Czy napotkałeś jakieś problemy podczas wdrożenia MES SoftLi?
Jest jedna komplikacja, ale nie jest to wina MES. PPF ma standard prezentacji, którego musi przestrzegać każdy oddział. Nie kierujemy się tym, bo nie piszemy już markerami na tablicach i papierze, ale staramy się wszystko przenieść na ekrany. Wszędzie korzystamy z danych rzeczywistych i wizualnych. I jesteśmy za to karani. ????
Krótko mówiąc, w korporacjach przyzwyczajenie się menedżerów najwyższego szczebla do takich innowacji zajmuje czasem trochę czasu. Dlatego czasami uparcie obstają przy „starych, dobrych” metodach z ubiegłego wieku, choć robi się dokładnie to, o co postulowali wówczas japońscy specjaliści od Lean Production czy pionierzy Przemysłu 4.0, ale nie było to jeszcze technologicznie możliwe.
Teraz jesteśmy znacznie dalej od standardu, ale nie ma innego pola w ocenie na to w tabeli. W skali od 1 do 5 powinniśmy dostać 6, ale tego pola tam nie ma. Dlatego mamy obniżoną ocenę, bo tak naprawdę nie spełniamy standardów korporacji.
Czego najbardziej się obawiałeś podejmując decyzję o wdrożeniu MES?
Poznawałem wówczas PPF i nie wiedziałem, jakie są dostępne opcje. Próba wprowadzenia czegoś nowego wkrótce po dołączeniu do nowej firmy zawsze wiąże się z pewnymi obawami. Dodatkowo trzeba przekonać przełożonych, że jest sens realizować dane zadanie.
Oczywiście istnieją również obawy ze strony realizatorów. A jeśli firma nadal korzysta z Excela i nie ma nic na stanie, to dość trudno im powiedzieć: „Słuchaj, potrzebuję tak dużo do tego, tak dużo do tamtego, albo tak dużo do tamtego. Albo tyle w tym temacie. To zależy od tego, jak daleko chcemy posunąć się we wdrażaniu.”
W momencie mojego przyjazdu PPF było polem niezaoranym z punktu widzenia MES. Nie wiedziałam, jak daleko możemy się posunąć i czy moje wysiłki w ogóle zaowocują jakąkolwiek realizacją. Bardzo się tego obawiałem, bo w tym czasie firma potrzebowała też innych rzeczy – inwestycji w maszyny, regularnych przeglądów itp.
Co więc sprawiło, że Twój pomysł dostał zielone światło?
Mój szef idzie z duchem czasu i jest oświecony, więc kiedy pokazałem mu zasady MES od SoftLI i wszystko mu wyjaśniłem, od razu się w to wciągnął. Zainteresował się, coś przeczytał, porozmawiał ze znajomymi i zdecydował się na to. Uzgodniliśmy, że wykonamy pierwsze wdrożenie.
Jak poszło?
Pierwsze wdrożenia miały charakter próbny. Nie były więc bardzo drogie, ale dały szansę przekonania naszych bezpośrednich przełożonych i pokazania im korzyści płynących z systemu. To się udało, dlatego stopniowo rozszerzaliśmy MES na inne ważne dla nas procesy.
Co roku stopniowo dodawaliśmy kolejny moduł, czasem nawet dwa. A później wprowadzono niektóre moduły nawet poza budżetem, gdy okazało się, że MES pomoże nam rozwiązać jakiś bieżący problem – a nasi przełożeni zatwierdzili niezwykłą inwestycję. Byli bardzo mile zaskoczeni tym, co można to zrobić za pomocą MES.
Dziś firma jest już dobrze połączona, dzięki czemu możemy cieszyć się wszystkimi zaletami, jakie oferuje system i inwestować w inne projekty.
Wspomniałeś, że najwyższe kierownictwo było przekonane pierwszymi szybkimi korzyściami z wdrożenia próbnego.
Dla mnie osobiście dużym pozytywem było to, że mogłem zobaczyć dane zebrane podczas produkcji i natychmiast przeanalizować występujące problemy.
Przyszedłem do PPF z innego rodzaju produkcji i innego środowiska, więc najpierw musiałem szczegółowo zrozumieć, jak to tutaj faktycznie działa. Na przykład na porannych spotkaniach omawialiśmy, co wydarzyło się poprzedniego dnia i nie za bardzo to rozumiałem.
Potem zobaczyłem dane dotyczące efektywności i dowiedziałem się, że było wiele krótkich przestojów w produkcji, które nie były nigdzie rejestrowane. Na przykład maszyna pracowała przez 2 minuty, po czym zatrzymała się na minutę, następnie pracowała przez 3 minuty i pracowała dalej przez kolejne 30 sekund.
Podsumowując, jak na 24 godziny produkcji oznaczało to już naprawdę duży przestój, o którym operatorzy nie wspominali w odręcznych zapisach. Dopiero na podstawie prawdziwych danych mogłem stwierdzić: „Tutaj jest problem i musimy się skupić na tym i tamtym”.
Mając wiedzę o podobnych analizach, mogłem pokazać swoim przełożonym: „Spójrzcie, ta maszyna ma najwyższy wskaźnik awaryjności. Przyjdź, zainwestuj w to i naprawmy to.”
Dzięki twardym danym udało nam się dokładnie wykryć, co jest zepsute, niesprawne lub na skraju przydatności do użytku – a następnie skutecznie zainwestować w naprawę lub wymianę maszyny. Wiemy więc, jakie problemy się pojawiają i jak je poprawnie rozwiązać. A nasza efektywność i skuteczność stale rośnie.
Czy można oszacować, ile zaoszczędzono dzięki wprowadzeniu MES? Jak wzrosła wydajność i skróciły się przestoje?
W naszym typie produkcji trudno to dokładnie określić ilościowo. Jesteśmy bardzo skupieni na kliencie i jego potrzebach, dlatego nasze portfolio produktowe stale się zmienia w zależności od jego wymagań. Co kwartał zmieniamy aż 20% portfolio. A każdy produkt niesie ze sobą nieco inne i specyficzne problemy...
Dlatego nie można jednoznacznie stwierdzić, że mamy np. 10% poprawę wyników w parametrze OEE, bo pojawiają się nowe trudności przy wprowadzaniu nowych produktów, co nagle nieco zaburza metrykę OEE.
Ogólnie jednak mogę potwierdzić, że w ciągu ostatnich 5-6 lat zwiększyliśmy produktywność o około 20%.
Wspomniałeś, że masz już doświadczenie we wdrożeniach MES z poprzedniej pracy. Czy możesz porównać te dwa procesy?
W poprzednim przedsiębiorstwie wdrażałem MES z dużą międzynarodową firmą, natomiast w PPF wybraliśmy mniejszego dostawcę i muszę przyznać, że dużo lepiej mi się pracuje. Duża firma nie może sięgać do swoich procesów i nie może skutecznie dokonywać żadnych dostosowań, które modyfikowałyby system zgodnie z potrzebami klienta.
W SoftLi zawsze zgadzacie się na personalizację pod moje wymagania, mimo że nadal działamy w ramach jakiegoś standardu. Wasza elastyczność jest zupełnie inna niż w przypadku dużych dostawców, dzięki czemu nie muszę borykać się z problemami, jakie mają nasze siostrzane zakłady u innych dostawców.
Wsparcie ze strony SoftLi jest maksymalne. Kiedy potrzebuję pomocy, dzwonię i od razu otrzymuję odpowiedź.
Jaki inny moduł planujesz na przyszłość?
Dla mnie to moduł jakości - moduł dokumentacji produktu, list kontrolnych i formularzy. Nie mogę się doczekać, aby nasza produkcja była jeszcze bardziej wydajna dzięki szczegółowym zapisom i dokumentom produkcyjnym opartym na zapisach temperatur, danych dotyczących wilgotności i innych danych.
Dziękuję za wywiad.
Czy Ty również chcesz zwiększyć produktywność?
Pomagamy małym i dużym firmom produkcyjnym zwiększyć wydajność nawet o 20%. Bez biurokracji. Bez przestojów. Bez wymówek.
Wypróbuj DEMO MES firmy SoftLi i przekonaj się sam.