AS-CASTING
Jak MES SoftLi zwiększył moce produkcyjne AS-CASTING o wartości 850 tysięcy złotych rocznie
„MES SoftLi to niewyczerpane źródło cennych informacji, do których mamy dostęp zarówno w czasie rzeczywistym, jak i wstecz. Dzięki niemu jesteśmy jedną z niewielu odlewni, które mają dodatni wynik finansowy. Bez MESu bylibyśmy na minusie.”
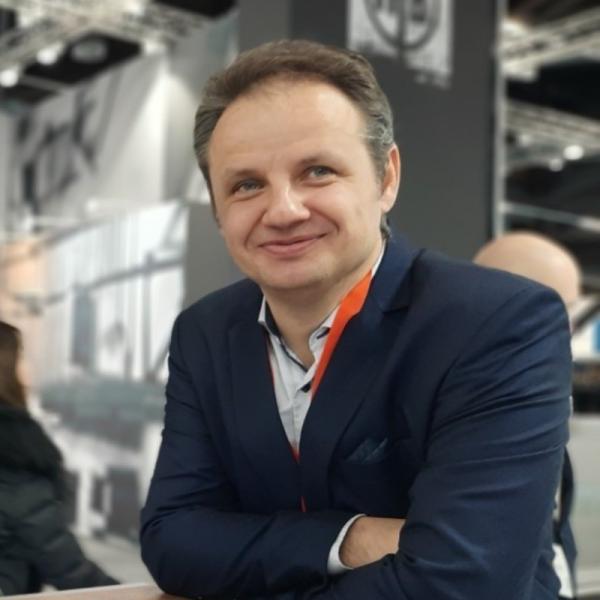
Jiří Zdražil, dyrektor zarządzający
Odlewnia AS-CASTING produkuje ciśnieniowe odlewy z pięciu stopów aluminium. Specjalizuje się głównie w branży motoryzacyjnej, do której trafia 60% produkcji. Reszta rozdzielana jest między przemysł elektryczny i spożywczy.
Produkcja odbywa się wyłącznie w trybie wieloseryjnym, gdzie każda partia to co najmniej 10 000 sztuk.
Zakład działa na 6 maszynach odlewniczych, pracujących non stop przez 340 dni w roku, odlewając produkty o wadze od kilku gramów do 7 kilogramów.
Odbiorcami odlewów są firmy montażowe, które dalej dostarczają komponenty bezpośrednio do producentów samochodów, m.in. Lear, Faurecia i Brano (produkcja radarów, belek poprzecznych i systemów drzwiowych).
Sytuacja przed wdrożeniem: ERP, Excel i zaufanie do ludzi
W AS-CASTING korzystano wyłącznie z systemu ERP Helios, który co 12 godzin generował raporty produkcyjne - ile wyprodukowano, ile było braków i jak wyglądało wykonanie norm.
Dwa główne problemy:
Dane były analizowane dopiero następnego dnia lub po weekendzie;
Wszystkie dane były wprowadzane ręcznie.
Po każdej zmianie pracownik wpisywał ręcznie wyniki do systemu, ERP liczył normy, a kierownik wklejał dane do Excela.
Kierownictwo wiedziało, ile wyprodukowano, ale nie wiedziało, dlaczego nie więcej.
„Musieliśmy wierzyć kierownikom i ich tabelkom. A bywało ciekawie,” mówi Jiří Zdražil.
„Na przykład zdarzyło się, że jedna maszyna zacinała się sto razy z rzędu co minutę. Brygadzista wpisał do tabeli tylko sto razy ‘awaria’. W ogóle nie interesował się, o co chodzi, dlatego zajęło nam kilka dni, zanim odkryliśmy, że maszyna się przegrzewa,” dodaje Zdražil, wspominając też o innym problemie.
„Ręczne wpisywanie liczby wyprodukowanych sztuk czasami kusiło niektórych pracowników do oszustwa. Gdy norma wynosiła 1000 sztuk na zmianę, a oni mieli tylko 900 albo 950, myśleli, że to się gdzieś zgubi i wpisywali, że normę zrealizowali. Ale liczby się nie zgadzały i nie dało się ustalić, gdzie popełniono błąd.”
Czasami pracownicy popełniali błędy w ręcznym zapisie produktywności nieumyślnie.
Wypełnili go błędnie. I zamiast wpisać 1000 wyprodukowanych sztuk w ciągu 12 godzin, przez pomyłkę podali, że w trakcie tysiącgodzinnej zmiany wykonali 12 wyrobów.
To oczywiście spowodowało zamieszanie w systemie i konieczne było wdrożenie systemu pośredniego, aby tego typu wpadki można było później korygować.
„Na początku, kiedy mieliśmy tylko 2 linie, teoretycznie dało się jeszcze zapamiętać wszystko, co wydarzyło się podczas zmiany. Ale po rozbudowie produkcji nie było już na to szans. Dodatkowo raportowanie, ze względu na konieczność przypominania sobie szczegółów i późniejszego ręcznego przepisywania do tabeli, było nieproporcjonalnie czasochłonne,” wyjaśnia Jiří Zdražil, dyrektor zarządzający AS-CASTING.
A kiedy w ramach rozbudowy dodano poza główną halą produkcyjną szóstą maszynę, stało się jasne, że zmiana jest nieunikniona.
MES z Niemiec przyniósłby więcej szkody niż pożytku
W odlewni przez kilka lat szukano odpowiedniego systemu MES. Początkowo rozważano niemiecki system, opracowany przez firmę, która sama prowadzi odlewnię. Problemem jednak była wysoka cena i bariera językowa.
„Ci, którzy znają języki obce, pracują w dziale handlowym, natomiast technolodzy, którzy obsługują MES i muszą z niego korzystać, nie znają wystarczająco dobrze niemieckiego,” wyjaśnia Zdražil.
Dyrektor zarządzający AS-CASTING po analizie rynku pod koniec 2022 roku zdecydował się na MES SoftLi.
Wdrożenie przebiegło szybko, ale mogło być jeszcze szybsze…
…gdyby odlewnia miała własnego informatyka, a nie tylko zewnętrznego doradcę IT dostępnego telefonicznie. Dlatego trzeba było najpierw rozwiązać problem z brakiem przygotowania zarówno po stronie oprogramowania, jak i sprzętu.
Poza tymi kilkoma szczegółami, które – jak mówi Jiří Zdražil – nie będą dotyczyć firm z własnym działem IT, wdrożenie przebiegło bez komplikacji.
MES SoftLi zwiększa wydajność odlewni o 5%
Kierownictwo odlewni wkrótce po wdrożeniu systemu zauważyło, że MES SoftLi nie tylko pomaga rozwiązać problem z monitorowaniem wydajności, ale też poprawia wydajność.
„Aluminium trzeba topić w ściśle określonej temperaturze – tego nie da się zmienić. Ale można w tym samym czasie wyprodukować więcej,” komentuje Zdražil, wskazując na priorytety firmy z Nowin pod Ralskiem.
Chociaż ich produkcja odbywa się obecnie w kilku pomieszczeniach, technolodzy i kierownicy mogą monitorować cały zakład w czasie rzeczywistym i mają wgląd także w powiązane operacje.
MES SoftLi pokazuje im na przykład, ile materiału znajduje się aktualnie w poszczególnych maszynach.
Pracownikom wystarczy spojrzeć na tablicę.
Po kolorze można łatwo rozpoznać, czy zbiornik jest:
pełny - zielony
w połowie pełny - pomarańczowy
pusty - czerwony
„Uzupełnianie trwa 20 minut, dlatego trzeba zacząć z odpowiednim wyprzedzeniem, aby nie dochodziło do przestojów. Wcześniej się zdarzały, ale dziś wystarczy, że kolor przy dowolnej maszynie zmieni się z zielonego na pomarańczowy – i ludzie od razu wiedzą, co mają robić. Kiedyś skarżyli się, że nie mają takich informacji, ale dziś podstawowe instrukcje automatycznie zadaje MES,“ dodaje dyrektor AS-CASTING.
Udało się również wyeliminować przestoje podczas zmian.
Pracownicy przekazują sobie maszyny „w biegu“, bez całego rytuału:
wyłączenia
przerwy na papierosa
ponownego włączenia
nagrzewania i produkcji kilku braków
Jak już wcześniej powiedział Jaroslav Ordelt z firmy SumiRiko w innym case study: Sama świadomość, że przełożeni mogą w czasie rzeczywistym, jak i z perspektywy historii, monitorować całą aktywność przy maszynach - działa cuda.
Według dyrektora odlewni wdrożenie MES SoftLi pozwoliło zredukować na każdej zmianie przy każdej maszynie 30 minut przestoju. W sumie to aż 6 godzin dziennie.
Koszt pracy jednej maszyny to 430 PLN na godzinę, więc każdy przestój ma znaczenie:
430 PLN/h * 6 maszyn = 2 580 PLN dziennie
2 580 PLN * 30 dni = 77 400 PLN miesięcznie
Odlewnia zwiększyła więc swoją zdolność produkcyjną o ponad 77 tysięcy złotych miesięcznie.
Nie zawsze udaje się ją w pełni wykorzystać, ale daje to przestrzeń do zarobienia nawet o 80 tysięcy miesięcznie więcej.
„Osiągnęliśmy wzrost produktywności o 5%, bez większego wysiłku i bez naciskania na ludzi,“ podsumowuje Zdražil.
Według dyrektora AS-CASTING system MES ma jednak pozytywny wpływ także na jeden całkowicie niewytwórczy aspekt.
Relacje z klientami.
MES poprawia także wizerunek firmy
Klienci AS-CASTING przeprowadzają w odlewni co najmniej 10 audytów rocznie, aby osobiście sprawdzić, gdzie i jak przebiega produkcja zamawianych przez nich wyrobów.
W przeszłości wszyscy zadawali to samo – absolutnie kluczowe – pytanie: Jak planujecie produkcję?
Od trzech lat już go nie zadają.
„Jeśli podczas audytu uda się przekonać klientów, że macie dobrze zorganizowaną produkcję, to wygraliście,“ wyjaśnia Jiří Zdražil.
Odlewnia otrzymuje bardzo pozytywne opinie na temat monitorowania produkcji od swoich klientów. Dziś nie trzeba im już nic tłumaczyć – wystarczy włączyć SoftLi Raportowanie, pokazać ich zlecenie i wszystko staje się jasne.
Bez papierowa produkcja jest równie ważna jak dobre planowanie
Zdražil odczuwał ze strony klientów presję także na wdrożenie produkcji bez papieru – tak, aby wszystko było w komputerze. Dlatego podczas audytów pokazuje również, jak wykorzystują rozszerzający moduł Formularze
I znów z doskonałym feedbackiem.
W przeszłości odlewnia borykała się z problemem, że co 2 godziny w ramach kontroli jakości trzeba było podejść do każdej maszyny i zapisać wybrane parametry, ale:
nie działo się to dokładnie co dwie godziny
dane były niedokładne, a czasem wręcz zmyślone
inny pracownik musiał potem przez 2 godziny dziennie przeglądać papierową dokumentację.
Dziś na terminalach operatorskich mają zdefiniowane całkowicie „idiotoodporne” formularze, tak że np. przy pomiarze kontrolnym każdy pracownik od razu widzi, że tolerancja wynosi od–do, i nie wpisze wartości spoza tego zakresu.
Odlewnia w ten sposób przechodzi na całkowicie bezpapierową produkcję.
A poza papierem, nie używa już nawet Excela.
Tylko MES SoftLi i ERP – i to jedynie po to, by sprawdzić, czy ktoś gdzieś się nie pomylił.
Podsumowanie wyników wdrożenia MES SoftLi
Wzrost produktywności o 5%
Przejście na produkcję bez papieru
Usprawnienie organizacji i planowania produkcji